Tips For Operating Norms Of Liquid Silcione Plastic Injection Molding Machine
February 26, 2024
1. Molding temperature adjustment:
Before adjusting the injection molding machine, first confirm what material is used for the product, and set the heating temperature of the machine material tube according to the melting point of the material. Usually, the temperature of the feed nozzle (first section) is set low, the sol temperature (sections 2-4) is set high, and the discharge opening The temperature (end stage) is low. Jinyu Machinery automatic injection molding machine.
2. Mold opening and closing pressure setting:
Adjustment of mold opening and closing pressure: low-pressure mold clamping pressure. High-pressure mold clamping pressure is especially important to protect the mold. The lower the pressure, the better. Low-pressure mold clamping can be adjusted to the minimum pressure to lock the mold. The maximum pressure cannot exceed 20%.
The high-pressure clamping pressure depends on the size of the mold and the clamping tonnage of the machine. The high-pressure mold clamping can be adjusted to the minimum pressure so that the mold can lock the product without flashing. Usually the high-pressure clamping pressure is 50%-80% of the machine pressure (depending on the matching of the mold and the machine). When the product is defective, the high-pressure clamping pressure can be moderately relaxed with the consent of the superior supervisor. However, the high-pressure clamping pressure cannot exceed 95% of the machine pressure. Otherwise it will affect the life of the mold and machine. The mold opening and closing pressure of other sections is generally 30%-60% of the machine pressure. If it exceeds 60%, the mold or machine must be inspected.
3. Adjustment of mold clamping position.
The low-pressure mold clamping position should be adjusted according to the size and height of the product. The low-pressure mold clamping position is too small. If there are foreign objects larger than this position, the purpose of low-pressure protection will not be achieved. If the low-voltage clamping position is too large, it will waste time. The high-voltage switching position is too large. If there is foreign matter in the position smaller than this position, the low-voltage protection purpose will not be achieved. If the high-voltage switching position is too small, it will be detrimental to the machine's mold closing.
The usual adjustment method for low-pressure protection: Adjust the low-pressure position according to the size of the root product. Return the high-pressure position to zero. Manually close the mold until the mold cannot be completely closed (judgment method: there is no pressure display on the pressure gauge during mold clamping. The machine crank arm cannot be straightened) . Observe the actual mold closing value on the machine operation panel and then set the high pressure position. The set value is 0.2-0.5mm larger than the actual value (different brands of machines have different adjustment methods).
4. Adjustment of mold opening and closing speed:
The opening and closing speed should be adjusted according to the principle of slow and fast. When the mold structure is complex (with a slider), slow-speed switching of the mold should be used to avoid damaging the mold during the switching action. When closing the mold, the mold should be closed at a low speed when it enters the low-pressure section. Usually the low-pressure mold clamping speed is 10%-40%. The high-pressure mold clamping speed is 20%-50%.
5. Adjustment of thimble action
The ejection speed should not be too fast and the pressure should not be too high. It should be smooth and gentle. The ejection length should not be too long and should be set from short to long during debugging. It is better to be able to eject the finished product and the nozzle smoothly.
6. Injection molding parameter adjustment
Sol parameter setting:
The position of the sol is estimated based on the weight of the product and the size of the screw on the machine. When adjusting, set a reasonable sol position from short to far according to the machine operation display screen. Do not set the melt pressure too high. It is generally set to 80Bar-120Bar. The melt speed setting is generally 30%-80% (depending on different materials and product appearance requirements). Jinyu Machinery Lsr Injection Molding Machine
Injection speed setting:
The speed at which the melt flows in the mold cavity determines the depth and gloss of the fusion line of the part, as well as surface defects such as scorching, chipping, and flow marks caused by poor exhaust. Usually, the adjustment method is based on the principle of slow (gate), fast (middle of the product), and slow (end of the product). Then adjust according to the surface requirements of the product.
Setting of injection pressure:
The pressure from the screw injection start position to the secondary pressure switching position. The injection pressure is responsible for converting the mold cavity into a holding pressure after the mold cavity is completely filled. If this pressure is too small, the parts will not be aligned, the fusion line will be deep, and the gloss will be too bright. . Excessive injection pressure will cause the mold to expand and the molded product to take off. During debugging, set the injection pressure appropriately according to the requirements of the product. The maximum injection pressure cannot exceed 95% of the machine system pressure.
Setting of injection position:
Different speeds of injection and different position changes determine the appearance of the product. According to the product appearance requirements, different speeds and pressures are used in segments to match the injection conversion position, and a reasonable injection position is set based on the machine display value and observation of the injected product. Usually, when adjusting the machine, the gate position is first found, and the gate is usually filled at a slow speed. Then switch the second stage position to fill the product at medium speed or fast speed. When the product is filled to about 90%, switch to low speed and reach the end position of injection molding (injection molding to pressure holding position or v-p switching position).
The final position is usually set to a standard of 95%-98% fullness of the injection molded product. It is most reasonable to observe the minimum margin of the injection screw (the most advanced position) of 5-10MM through the control panel, that is, the final position is 5-10MM. If the final position is too large, the product may be short of material. If the switching position is too small, the product will easily take off and have a greater impact on pressure transmission during pressure holding.
Note: Multi-cavity mold products that are adjusted for the first time cannot be filled with one injection. The injection position must be controlled to fill 30%, 50%, and 80% of the product in sequence and observe whether the glue in the product is balanced. If necessary, use an electronic scale to weigh it. .
Adjustment of injection time:
, the length of injection time depends on the injection position and speed. Determined by pressure and molding temperature. If the injection conversion mode is time control, the injection time should be set from short to long until the product mold retention reaches 95%-98% before switching to pressure holding. If the injection time of this method is too short, the product will easily run out of material. If the injection time is too long, the product will easily stick to the mold or become white. If the injection conversion mode is time + position or position control, the injection time setting should be 1-2 seconds longer than the machine display time.
Adjustment of retreat action:
Loosening can prevent "saliva" phenomenon, but will allow air to enter the barrel. The general setting pressure is 30-50Bar, the speed is 20%-30%, and the position is 3-10MM.
Adjustment of holding pressure:
The pressure from the injection pressure to the holding pressure switching position (S5) is called the holding pressure. After the injection pressure is adjusted appropriately, the size of the holding pressure determines the shrinkage (lack of material), peaking, flow lines and top of the product. Crack etc. Usually the holding pressure is adjusted from small to large according to the requirements of the product, and the holding time is set from short to long according to needs. The holding speed is usually 5%-30%. Note: When searching for the injection position, the holding action must be canceled (the holding pressure or holding time should be reset to zero).
Back pressure adjustment
, the back pressure is the pressure on the melt at the top of the screw when the screw rotates and retreats. Increasing the back pressure will increase the melt temperature, but will reduce the plasticization rate. It can make the melt temperature uniform, the materials can be mixed evenly, and the gas in the melt can be eliminated. Usually the back pressure of plastic is 5Bar-30Bar. If the back pressure is too large, the screw will not move back, and if the back pressure is too small, it will not be able to compress and mix the plastic.
Adjustment of the seat part:
For forward and backward movements of the platform, the pressure is usually set to about 30Bar and the speed is 10%-30%. Be careful not to apply too much pressure, otherwise the machine nozzle and mold nozzle will be damaged.
Adjustment of mold temperature:
Usually increasing the temperature of the mold has three effects. 1. The mold temperature is related to the glue flow speed. If the temperature is high, the glue will have good fluidity. If the temperature is low, the glue will have poor fluidity. 2. The surface finish of the product can be controlled by increasing the mold temperature. The higher the mold temperature, the smoother the surface of the product. 3. The size of the product can be adjusted appropriately by controlling the thermal expansion and contraction of the mold temperature.
7. Settings for injection molding monitoring during production:
Adjusting injection molding monitoring parameters during production is crucial to quality control. Injection molding monitoring parameters include monitoring of the remaining amount of injection molding (end position of injection), monitoring of injection molding time, monitoring of sol position and sol time. After adjusting the machine and producing 50 molds normally, the actual monitoring values are set by observing the machine monitoring screen. Usually the minimum position monitoring position of the injection screw is generally plus or minus 0.5-2MM. The sol time is plus or minus 1-3 seconds.
8. Confirm production:
After adjusting the machine to produce the finished product, you have to check the sample yourself first. If you think it is OK, you need to notify IPQC for inspection. After passing the inspection, you can notify the operator to produce. After the first piece is confirmed OK by IPQC, the first 10 molds and adjusted products will be scrapped as defective products to ensure that the products in production will not be mixed with defective products. During normal production, if three consecutive molded products are defective, you should exit the fort and check and analyze the reasons. After normal production, the process parameters should be saved in a timely manner and the process card should be prepared in a timely manner.
9. Things to note
When adjusting the injection molding machine, all pressures should be minimized to produce qualified products. All pressures should not exceed 95% of the system pressure without approval.
When the machine nozzle is blocked during machine adjustment, do not increase the injection pressure to flush out the blockage.
The mold must be kept closed when seated.
When adjusting the machine, the product must not be fully molded at one time to prevent parts from sticking to the mold.
When handling the mold, the base must be exited and the motor must be turned off.
When dealing with machine abnormalities, two people cannot operate the machine.
Do not operate the machine without training. Jinyu Machinery Liquid Silicone Rubber Injection Molding Machine.
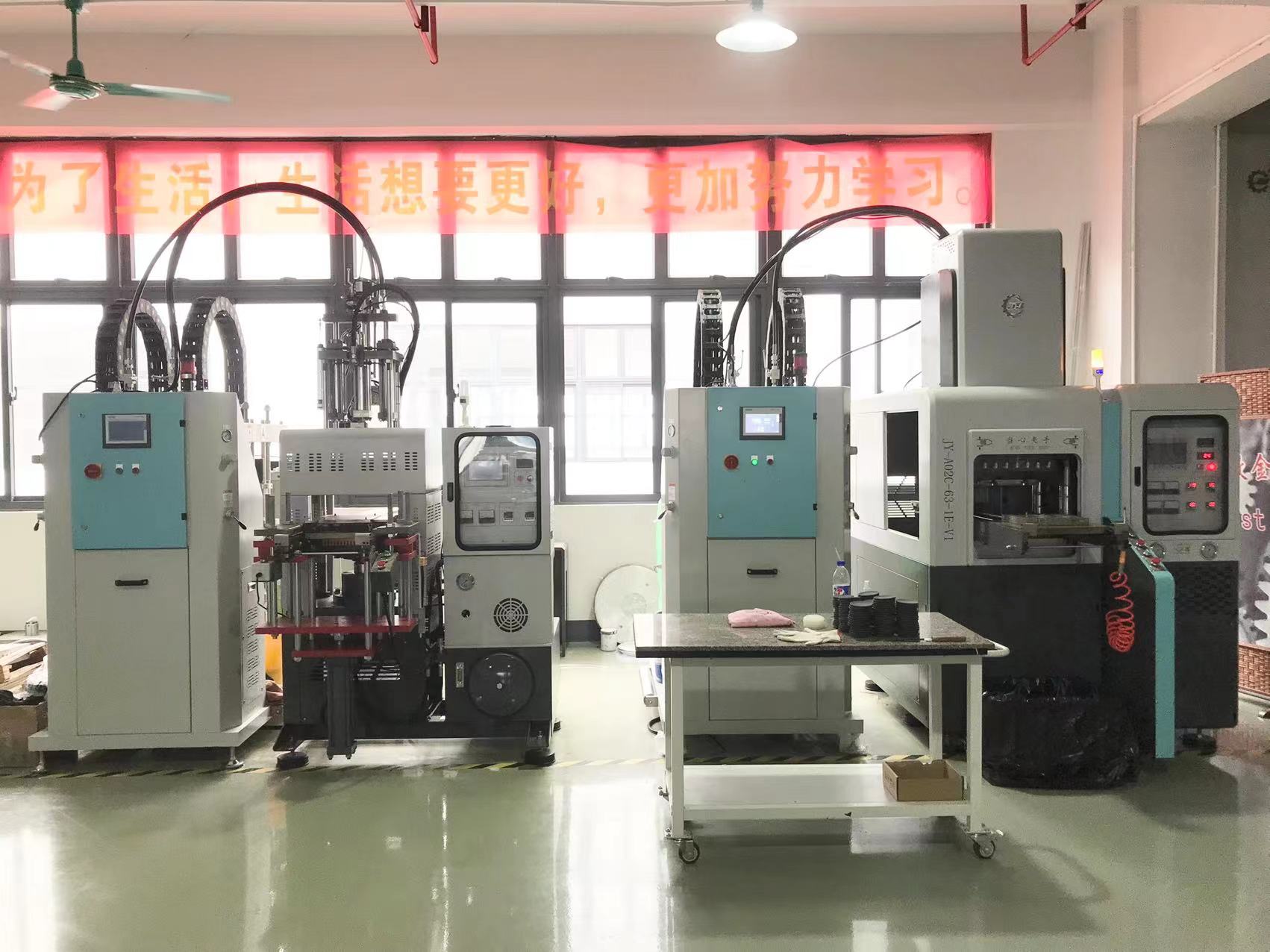